Газотурбинный кризис. Часть 1: Введение и советский период
Зависимость России от импорта газовых турбин и комплектующих — более 90%, в стране нет собственного производства турбин большой мощности, которые необходимы для работы современных ТЭЦ, газовых электростанций и газовых трубопроводов. Наложенные санкции перекрыли доступ к основным поставщикам газотурбинного оборудования. Как Россия попала в газотурбинную ловушку и как будет из нее выбираться? Разбираемся вместе.
Почему так важны газовые турбины?
Энергетические турбины — паровые и газовые — используются в качестве приводов электрогенераторов. Турбины представляют собой валы с одним или несколькими дисками с лопатками, пар или газ при своём стремительном движении в турбине обтекает эти лопатки и вращает диски, посаженные на вал двигателя (электрогенератора). В паровой турбине действует пар высокого давления, поступающий из парового котла. Газовая турбина работает за счёт струи раскалённых газов, получаемых от сжигания горючего в камере сгорания самой турбины.
Так без поступательного движения поршней, преобразуемого коленчатым валом и маховиком во вращение вала мотора, мы сразу получаем круговое вращение вала турбины.
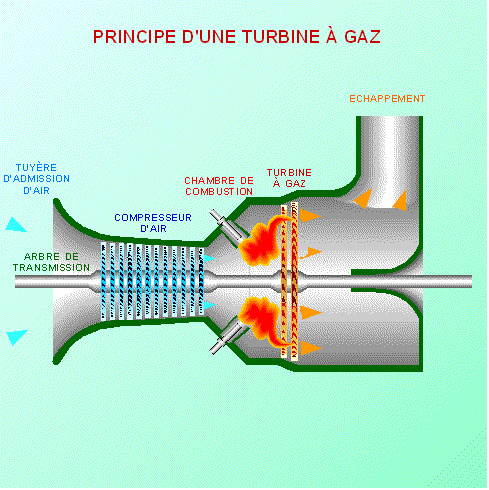
Различного типа газовые турбины используются в электростанциях для обеспечения населения светом и теплом, в транспорте, кораблестроении, авиации, насосных станциях для перекачки углеводородов в трубопроводах и других отраслях промышленности.
Изначально газовые турбины существенно уступали паровым, но со временем КПД и мощность газовых турбин увеличивалась и к 80-м годам они начали серьезно конкурировать с энергетическими установками, использующими пар. Комбинирование паровой и газовой турбины, где высоко температурные выхлопные газы газовых турбин направляются в специальный котел-утилизатор, производящий пар, который направляется на паровую турбину, привело к появлению высокоэффективных комбинированных парогазовых установок (ПГУ). КПД таких установок существенно превышал КПД существовавших в то время тепловых и атомных станций.
Сегодня в России работают около 250 импортных газовых турбин — это, по данным Минэнерго, 63% от общего количества. В основном это изделия производства компаний Siemens, General Electric, Alstom, Mitsubishi. В нашей стране доля газовой энергетики равна 60% (по миру в среднем - около 25%), а КПД лучших газовых ТЭС не выше 35%, а у средних и того меньше. У ПГУ же этот показатель превышает 50%. Так что внедрение ПГУ - один из немногих путей технологического перевооружения российской энергетики.
Но основная проблема заключается в том, что Россия серьезно отстала в создании энергетических газовых турбин большой мощности - ключевого элемента ПГУ.
Производство газовых турбин в СССР
В начале 1950-х годов быстрое расширение сырьевой базы для добычи природного газа и большой экономический эффект, полученный от его применения, со всей очевидностью выявили экономическую необходимость создания новой отрасли народного хозяйства – газовой промышленности.
В СССР разработка стационарных газовых турбин проходила по двум основным направлениям, в качестве:
приводов для компрессорных станций на газопроводах (Невский завод им. Ленина НЗЛ, Уральский турбомоторный завод)
энергетических установок для несения пиковых и полупиковых нагрузок (Ленинградский Металлический завод)
В СССР первые отечественные промышленные энергетические газотурбинные установки были выпущены в 1950-х. Эти установки ГТ-600-1,5; ГТ-700-4 мощностью 4 МВт (НЗЛ) и ГТ-12-3 мощностью 12 МВт с КПД 27% (ЛМЗ) были спроектрированы на умеренные начальные температуры газов (600–700°С). КПД первых установок были, как правило, ниже проектных из-за низких КПД компрессоров и турбин, повышенных утечек воздуха из трактов высокого давления, недостаточной эффективности регенерации.
Газоперекачивающие агрегаты (ГПА)
Наиболее оптимальным оборудованием для компрессорных станций (КС) магистральных газопроводов стали газоперекачивающие агрегаты (ГПА), состоящие из центробежных высокооборотных нагнетателей с газотурбинным приводом.
При строительстве газопровода Саратов – Москва использовались ГПА иностранного производства. Но уже совсем скоро стало ясно, что страна остро нуждается в отечественной газоперекачивающей технике.
Бригадир Буц К. К. и гл. инженер монтажного участка Никаноров А. А. за проверкой монтажа генераторов. Газопровод Саратов-Москва. 1946 г.
В 1945 г. конструкторы Невского машиностроительного завода им. В.И. Ленина начали разработку первой газотурбинной установки, которая была изготовлена к 1947 г. В 1952 г. создается первая отечественная стационарная газовая турбина ГТ-600 мощностью 1,5 МВт, а в 1956 г. было построено уже шесть промышленных газотурбинных установок.
Осмотр первой газотурбинной установки, спроектированной главным конструктором С.М. Жербиным 1947 г.
В 1958 г. было начато производство газовых турбин и стационарных газотурбинных установок (ГТУ) ГТ-700-4 для магистральных газопроводов, что и определило основной профиль деятельности завода в последующие годы. В 1959 году ГТ-700-4 впервые начали эксплуатироваться в первых газоперекачивающих агрегатах (ГПА). К 1965 году установленно 62 таких ГТУ суммарной мощностью 248 000 кВт.
Опыт эксплуатации ГПА данного типа на компрессорных станциях газопровода Саратов - Москва выявил их крупные недостатки (спроектированная одновальная энергетическая газовая турбина не была приспособленна к переменным режимам работы нагнетателя на магистральном газопроводе), но подтвердил перспективность применения газотурбинного привода нагнетателей природного газа. Это способствовало созданию новых типов размеров приводных ГТУ и их массовому производству, что обеспечило возможность сооружения первых магистральных газопроводов большой протяженности.
Стремясь устранить выявленные недостатки, на Ленинградском металлическом заводе разрабатывался газоперекачивающий агрегат ГТН-9-750, в 2,5 раза превосходивший по производительности нагнетания и мощности установку ГТ-700-4. С 1960-х впервые примененная в ГТН-9-750 схема с разрезным валом была принята как оптимальная во всех последующих газоперекачивающих агрегатах производства Невского машиностроительного завода.
Уральский турбомоторный завод им. К.Е. Ворошилова
В 1959 г. на вновь организованном после войны Уральском турбомоторном заводе им. К.Е. Ворошилова конструкторский коллектив приступил к проектированию газоперекачивающего агрегата (ГПА) мощностью 6 тыс. кВт собственной конструкции. К концу 1962 г. образец этого агрегата (ГТ-6-750) был изготовлен, а с 1965 г. было развёрнуто его серийное производство на Невском машиностроительном заводе и Свердловском турбомоторном заводе.
Несмотря на более низкий КПД, агрегаты, имели существенные компоновочные преимущества, которые снижали капитальные и трудовые затраты при сооружении компрессорных станций с данными газоперекачивающими агрегатами. Создание новой производственно-технической базы конструирования и изготовления газотурбинных ГПА стационарного типа обеспечило эффективную конкуренцию и ликвидировало опасную с точки зрения технического прогресса монополию Невского завода.
В 1968 году – на НЗЛ начат серийный выпуск самых массовых в СССР газоперекачивающих агрегатов мощностью 10МВт – ГТК 10.
ГТК 10 производства Невского завода им. Ленина
В 1974 году на НЗЛ создается Научно-исследовательский конструкторско-технологический институт турбокомпрессоростроения. Создается целая серия новых машин - разработан и изготовлен (взамен импортируемого) самый мощный в СССР газоперекачивающий агрегат нового поколения ГТН-25 мощностью 27,5 МВт, повышается мощность ГТК-10.
Однако выявленные в эксплуатации конструктивные недостатки агрегата ГТН-25, а главное технические сложности ремонта в условиях КС магистральных газопроводов, расположенных в труднодоступных районах Севера, не позволили перейти на крупносерийное производство ГПА нового поколения. Несмотря на это, применение данных газоперекачивающих агрегатов позволяло поддерживать экономику СССР путем их установки на экспортные газопроводы для транспорта газа, предназначенного европейским потребителям.
Монтаж газоперекачивающего агрегата ГТН-25. Компрессорная станция экспортного трубопровода Уренгой-Помары- Ужгород. Город Шемордан, Татарская АССР, РСФСР
В свою очередь, в 1983 году на Уральском турбомоторном заводе начато изготовление газоперекачивающих агрегатов ГТН-25-1. Несмотря на меньшее количество выпущенных агрегатов, их преимуществом являлся больший КПД по сравнению с ГПА аналогичной мощности производства Невского завода (31% против 25%). Впоследствии завод переквалифицировался на производство паровых турбин для парогазовых энергоблоков, конденсационных и теплофикационных турбин для паросиловых установок, судовых турбин для кораблей с атомной энергоустановкой.
Энергетические газотурбинные установки (ГТУ)
История проектирования и производства ГТУ на Ленинградском Металлическом заводе (ЛМЗ) началась с 1957 г., когда была создана первая ГТ-12-3 мощностью 12 МВт с КПД 27%.
Результатом накопленного опыта при создании первой турбины явилось создание в 1959 г. новой серии ГТУ типа ГТ-25-700 мощностью 25 МВт с КПД 28%. Прогрессивные решения конструкторского бюро были внедрены в 1962 году в серии из 10 агрегатов ГТН-9-750. В 1967 году для Краснодарской ТЭЦ была изготовлена самая крупная в мире газотурбинная установка ГТ-100-750 мощностью 105 МВт с КПД 28%.
Конструкторы — создатели первых газовых турбин. Ленинградский Металлический завод. 1970 год
11 ноября 1973 г. вышло распоряжение Совета Министров СССР о строительстве филиала ЛМЗ. Предусматривалось создание корпуса газовых турбин с испытательным стендом и блока заготовительных цехов.
В 1979 году принят в эксплуатацию 1-й пусковой комплекс газовых турбин, который получил название завод «Турбоатомгаз». В этом названии отражена основная задача предприятия – выпуск газовых и паровых турбин, агрегатов для АЭС.
Завод Турбоатомгаз в 2000-х, ЛО, Новое Девяткино
Парогазовые установки ПГУ
В России исследования комбинированных термодинамических циклов выполнены в ЦКТИ 1934 — 1940 гг. и продолжены в послевоенные годы. В 1944—1945 гг. в ЦКТИ А. Н. Ложкин разработал схему парогазовой установки со сгоранием топлива при постоянном давлении. Теоретические основы комбинированного парогазового цикла с высоконапорным парогенератором (ПГУ с ВПГ) были рассмотрены в работах ЦКТИ (А.Н. Ложкин, М. И. Корнеев, А.Э. Гельтман), что позволило повысить эффективность установки.
Первые в СССР эксперементальные парогазовые установки с высоконапорными парогенераторами производительностью 120 и 50 тонн/час (1 т/ч = 0,627 МВт) были введены в опытно-промышленную эксплуатацию в конце 1963 г. В течение 1964—1965 гг. оборудование ПГУ на 1-й Ленинградской Государственной Электрической Станции проработало около 4500 ч. За это время выработано более 100 млн. квт-ч электроэнергии при работе на газообразном и жидком топливах.
В 1964 г. были введены в работу две установки с высоконапорным парогенератором (ВПГ): на Надворнянской ТЭЦ и на Ленинградской ТЭЦ № 2. Первая из этих установок смонтирована на ТЭЦ Надворнянского нефтеперерабатывающего завода и вырабатывает не только электроэнергию, но и технологический пар давлением 0,4 МПа. Газовым контуром этой установки является ГТ-15 Ленинградского государственного машиностроительного завода «Экономайзер», который в основном занимался корабельными газотурбинными энергетическими установками. ГТУ выполнена по схеме со свободной силовой турбиной и при начальной температуре газа 973 К имеет мощность около 1500 кВт.
Экспериментальные ПГУ показали надежную работу установки во всем диапазоне нагрузок. Были продемонстрированы хорошие динамические качества ПГУ с ВПГ. Так, процесс запуска установки из холодного состояния до выхода на номинальную мощность составлял всего 40—45 мин.
На базе разработанных ЦКТИ схем и основного нестандартного оборудования парогазовых установок в Советском союзе были построены и введены в эксплуатацию парогазовые установки:
1963 г., Ленинград, 1-ая ЛенГЭС, ПГУ с высоконапорным парогенератором (ВПГ) - 6,5 мощностью 6,5 МВт (ηпгу =29,1%) на базе ГТУ-1,5 НЗЛ с начальной температурой газов 720°C;
1966-1970 гг., Ленинград, Блок-ТЭЦ №6, 3 блока ПГУ с ВПГ мощностью 16,5МВт, (η = 35,5%) на базе ГТ-700-4-1М НЗЛ с начальной температурой газов 700°C;
1972г , Невинномысск, Невинномысская ГРЭС, ПГУ с ВПГ мощностью 200МВт, (η = 43%) на базе ГТ-35 с мощностью 35 МВт с начальной температурой газов 770°C производства Харьковского турбогенераторный завода (ХТГЗ);
1982г, Молдавская ГРЭС, ПГУ с НПГ мощностью 250МВт, (ηпгу =42%) на базе ГТ-35 с начальной температурой газов 770°C. Годовая наработка блоков составляет 7460 часов. Блоки работают в переменной части графика электрических нагрузок с остановом газотурбинных агрегатов ГТ-35-770 ХТГЗ и разгрузкой паровых турбин К-210-130 до 40% от полной мощности на ночь. Отработаны режимы автоматического пуска ГТА и их подключения к действующим паровым котлам после ночного останова. Среднеэксплуатационное снижение удельного расхода топлива по сравнению с паросиловой установкой составляет 3-5%;
1990 г., на ГРЭС-3 заработала первая в России газотурбинная энергетическая установка парогазового цикла производства ЛМЗ — ГТЭ-150 мощностью 148 МВт с КПД 31%, после модернизации две ГТЭ-150 работают до сих пор.
1996г., ОПКС "Грязовец", ПГУ с КУ мощностью 35 МВт, (η =37,4%), на базе ГТН-25 НЗЛ с начальной температурой газов 770°C;
В 1957 году в основанном советским академиком С. А. Христиановичем новом Институте теоретической и прикладной механики СО АН СССР в Новосибирске по его же руководством ведется создание мощной энергетической экологически чистой парогазовой установки (ПГУ), которая могла стать основой экологически безопасных тепловых электростанций. Установка, разработанная под руководством С.А. Христиановича, при меньшем КПД позволяла существенно снизить расчетные затраты на производство электроэнергии на станции мощностью 1200 МВт. В 1965 году в институте завершалось сооружение уникального стенда ПГУ, представлявшего собой сложный дорогостоящий комплекс.
Сергей Алексеевич Христианович (в центре) с коллегами на стенде ПГУ
В институте за короткое время были подготовлены исходные данные для создания проектных заданий на ПГУ-200-750/70 для Айри-Байрамлинской ГРЭС и разработан совместно с рядом других организаций эскизный проект ПГУ-200-750/30 с парогазовыми турбинами на природном газе.
Однако, не дождавшись ввода в эксплуатацию экспериментального стенда ПГУ, в 1965 году из-за нарастающих личных противоречий в отношениях с академиком М.А. Лаврентьевым, по настоянию которого он был отстранен от обязанностей заместителя председателя СО АН и выведен из Президиума СО АН, Христианович возвращается в Москву.
С приходом в августе 1966 г. в ИТПМ СО АН СССР нового руководителя ⎯ академика В.В. Струминского тематика работ института резко повернула в сторону расширения аэрогазодинамических исследований и создания перспективной аэродинамической базы. Вскоре все оборудование ПГУ было демонтировано. Часть ведущих сотрудников, тесно связанных с тематикой ПГУ, ушла из института, а остальные переключились на новые исследования, связанные с решением проблем создания сверхзвуковых и гиперзвуковых летательных аппаратов.
Работы, выполненные коллективом ученых под руководством Христиановича в области экологически чистой энергетики, послужили толчком к активизации работ в этом направлении во всем мире и ПГУ получили распространение в странах Западной Европы и США.
Объем выпуска газовых турбин был небольшим, потому что основной акцент делался на серийное производство машин для паротурбинных энергоблоков. Это требовалось, чтобы обеспечить рекордные темпы ввода электрической и тепловой мощности, необходимой для развивающейся экономики страны.
Совместное предприятие ЛМЗ и Siemens
С развалом СССР в Санкт-Петербурге в 1991 году создается совместное предприятие по сборке из готовых компонентов энергетических газотурбинных установок Siemens V94.2. С этого момента ЛМЗ перестал производить собственные газовые турбины...
Продолжение следует...
Во второй части: СП ЛМЗ с Siemens, Крымский скандал, Санкции
Список литературы:
http://gtt.ru/wp-content/uploads/files/primeri/Catalogue-201...
https://www.tek-all.ru/news/id8026-silovie-mashini-sozdaut-o...
http://www.combienergy.ru/stat/900-Istoriya-parogazovogo-cik...
СОВЕРШЕНСТВОВАНИЕ ТЕХНИЧЕСКИХ ХАРАКТЕРИСТИК ГАЗОТУРБИННЫХ ГАЗОПЕРЕКАЧИВАЮЩИХ АГРЕГАТОВ КОМПРЕССОРНЫХ СТАНЦИЙ МАГИСТРАЛЬНЫХ ГАЗОПРОВОДОВТекст научной статьи по специальности «Энергетика и рациональное природопользование» Хасанов Ильнур Ильдарович, Шакиров Руслан Азатович, Жильцова Анастасия Юрьевна, Каширина Дарья Алексндровна
Исторические аспекты производства газоперекачивающего оборудования и обеспечение энергетической безопасностиТекст научной статьи по специальности «История и археология» Грибов Роман Викторович
https://www.studmed.ru/view/arsenev-lv-tyryshkin-vg-kombinir...
https://flotprom.ru/publications/science/engine/introduction...
Известный ученый-механик ХХ века