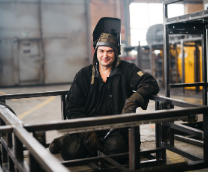
Сделано в России
41 пост
Два месяца назад мы уже приезжали с вами в Исправительную колонию № 7 Управления Федеральной службы исполнения наказаний по Ивановской области (если впервые читаете, то рекомендую загуглить «Спектакль в женской Исправительной колонии № 7»). И сегодня в преддверии приближающихся праздников тоже там побываем на одном ярком мероприятии.
Обещаю, что вы увидите много знакомых лиц с прошлой поездки, но уже в новых образах
Напомню, что это женская колония в которой на сегодняшний день чуть более 500 осужденных. Отбывают заключение уже ранее судимые. Более 50% сидят по статье за наркотики, но в целом есть все статьи от мошенничества до убийств.
Основной вид деятельности - швейное производство (ассортимент большой и включает в себя от изделий вещевого довольствия сотрудников УИС и спецконтингента до форменной, специальной и рабочей одежды).
Кроме работы тут еще получают образование: есть вечерняя школа для не достигших 30-летнего возраста и ПТУ, где осваивают профессии швеи, повара, оператора газовой котельной.
В свободное же время заключенные участвуют в культурно-массовых и спортивно-оздоровительных мероприятиях. Для чего это проводят? В документах сказано: «для рационального использования свободного времени, развития творческих способностей и укрепления дисциплины». Но лично в моем понимании, это делается, чтобы человек в 4 стенах мог оставаться человеком (и кукушечка у него в голове не отъезжала) и после освобождения у него был еще один шанс на нормальную жизнь. И если гражданочка сможет, уцепившись за творчество (начиная от рисования и заканчивая пением с танцами), сохранить в себе веру, что прекрасное далеко не будет с ней жестоко — может и жизнь станет другой. Скорее всего я идеалист и верю в перевоспитание, но в системе есть не только наказание, но и исправление.
Но я увлекся (как всегда). Возвращаемся в ИК №7
В этот день нас ждет «Кулинарный поединок». Заходим в столовую. Она уже декорирована под кафе из 80-х. Все сделано руками осужденных.
Три команды уже готовы. На пищевом ринге нас встречают: «Гигинты из кафе минутка», «Гости из прошлого» и «Кафе причал». В каждой по 4 повара.
Каждая команда должна приготовить три блюда: салат, горячее и десерт за ограниченное время.
Пока происходит кулинарное действо - для жюри, гостей и зрителей из числа заключенных показывают музыкальные и танцевальные номера, подготовленные специально для новогоднего мероприятия.
Все костюмы на участницах команд и в творческой части полностью созданы заключенными.
Все блюда выглядели очень приятно. При каждой подаче участницы из команд рассказывали небольшую историю и информацию о продуктах и рецепте.
Попробовать всю эту вкусноту, к величайшему моему сожалению, у меня не вышло — в жюри все места были заняты (на самом деле просто не получилось бы тогда сделать все эти фотографии, поэтому выбрал пищу творческую, а не обычную), так что пришлось довольствоваться рассказами известного в регионе художник-коллажиста, о том, что все было вкусно.
Творческие номера как всегда в этой колонии на высшем уровне. Когда-нибудь в заявке на технику укажу не только фотоаппарат, но и гоупрошку, и покажу вам клипы с выступлений.
В финале поединка победу одержала команда «Гигинты из кафе минутка», поварам из команды «Гости из прошлого» досталось второе место, участники из «Кафе причал» получили третье место.
P.S. По традиции всегда указываю это в постах из колоний - в нашем регионе прокуратура всегда очень внимательно следила за соблюдение прав осужденных, так что уточняю: в колонии заключенных можно фотографировать только с их письменного согласия. Все участницы моего фоторепортажа его подписали. И эти документы есть в учреждении
Сегодня мы увидим как происходит оцинковка металла на Череповецком металлургическом комбинате. Нас ждет бассейн расплавленного цинка, огромное «зеркало» высотой в дом, робот-манипулятор и манящая бадейка с гартцинком. Вы готовы? Тогда отправляемся в Череповец.
Цех покрытий металла №3 знаком нам по прошлому посту с полимеризацией. В него же входит агрегат непрерывного горячего цинкования №4.
Кроме горячего цинкования существуют и другие варианты: холодное, гальваническое, термодиффузионное и газотермическое. У каждого есть свои плюсы и минусы.
Но мы сегодня «в гостях» у горячего цинкования.
Пройдем к начальному этапу агрегата.
По дороге нас встречают огромные слитки цинка.
Рулоны стали поступают сюда после Стана-2000 (очень рекомендую о нем почитать у меня несколько постов назад, это нечеловечески крутая машина)
Как и на агрегате полимерных покрытий тут для непрерывности установлены два разматывателя, для непрерывной работы. Пока один рулон разматывается, второй уже устанавливается.
Максимальная масса рулонов тоже до 30 тонн
Кроме разматывателя, осуществляющего размотку рулонов, на этом участке установлена листоправильная машина (для правки переднего и заднего конца полосы с целью задачи полосы в отрезные ножницы), гильотинные ножницы (для обрезания концов полосы, имеющих дефектные участки и отклонение от требуемой толщины), сварочная машина (для сварки заднего конца предыдущего рулона и головного конца следующего рулона выпрямленным током с раздавливанием кромок стальных полос), вырубной пресс (для вырубки метки на полосе в районе сварного шва) и натяжная станция №1 — для создания заданного натяжения полосы в головной части.
До химического узла установлено петлевое устройство №1. Оно предназначено для создания резерва полосы, чтобы обеспечить работу участка на нужной скорости, когда работа участка ввода технологической линии остановлена для смены рулона.
Полезная емкость такого накопителя 423 метра. А максимальная скорость 240 м/мин
Поверхность полосы металла должна быть подготовлена соответствующим образом для цинкования.
По этой причине ее подают на химический узел. Там происходит очистка от жировых и механических загрязнений.
При помощи 6 пар щеточно-моющих роликов осуществляется механическая очистка. А химическая путем распыления щелочного раствора на полосу через форсунки (отжимные ролики потом все убирают)
Далее в секции окончательной промывки с полосы смываются все остатки раствора. Горячий воздух высушивает полосу.
Теперь полоса заходит в печь термохимической обработки. Благодаря чему повысится адгезия поверхности с жидким цинком.
В камере предварительного нагрева полоса нагревается до 250-270 градусов.
В камере безокислительного нагрева нагревается уже до 650-750 градусов.
А в камере восстановительного нагрева полоса нагревается в зависимости от назначения от 730 до 780 градусов. За этим следует камера выдержки, где поддерживается температура 730-780 градусов.
В финале полоса охлаждается до температуры расплава цинка 460 градусов в камере струйного охлаждения.
Перейдем на самое зрелищное для меня место в цеху — в участок нанесения покрытий.
После термической обработки наша полоса, не соприкасаясь с воздухом, поступает в ванну с цинковым расплавом.
Внешне кажется, что поверхность ванны не особо большая, но в реальности ее вместимость 280 тонн расплава цинка.
Полоса на выходе из ванны напоминает огромный зеркальный столб.
А сама поверхность расплавленного цинка так и манит к себе. Жаль ее температура в 460 градусов ограничивает все возможные контакты с ней
В процессе оцинковки полосы остаются отходы — изгарь (на поверхности), гартцинк и нашатырный шлак.
Изгарь и гартцинк содержат цинк. И если в первой это 55%, то во втором до 90-97%. Есть даже технологические способы извлечения оттуда цинка.
Но его же еще надо достать из этого бассейна. Пару лет назад этим занимался специально обученный человек в костюме и с титановым черпаком.
С весны 2021 года этим занимается робот-манипулятор. Своим ковшом он производит уборку с зеркала расплава. Это еще один пример, как технологии упрощают жизнь человеку.
Кстати, то корытце с гартцинком и изгарью на главной фотографии поста и есть продукт работы робота.
После нанесения покрытия лента поступает на 33 метровую башню охлаждения.
На начальном участке происходит охлаждение до температуры, при которой не повреждается роликами поверхность. А затем и до температуры, необходимой для водяной закалки (где она в свою очередь охлаждается от 150 до 45 градусов).
Наступает этап правильно-дрессировочного стана и изгиборастяжной машины. Это нужно для изменения внутренних натяжений металла.
После всех процедур на узле нанесения пассивации, на металл наносится тонкая пленка из оксидов хрома. Далее лента отправится в печь сушки.
Пройдем ближе к завершающим этапам.
Нас встречает еще один вертикальный петлевой накопитель, обеспечивающий как и первый непрерывность и стабильность работы.
Его вместимость 280 метров.
До смотки полосы в рулоны она проходит через помещение инспекции выходного участка.
Тут установлены несколько оборудованных мест контроля. На части из которых выведены данные с многочисленных датчиков системы по цифровому контролю качества.
О ней подробнее рассказывал в посте про полимеризацию и не вижу смысла дублировать информацию.
На выходе после аттестации на металл наносят защитный масляный слой на промасливающей машине.
На выходной полосе полосу обрезают при помощи барабанных ножниц. Сама смотка происходит на моталках.
Краном рулон передается на упаковку. И тут уже в зависимости от пожеланий заказчика его упакуют в те или иные упаковочные материалы.
Впереди склад готовой продукции и доставка покупателю.
Вот такая небольшая, но интересная экскурсия получилась. Но на Северстали еще много всего интересного, так что буду веровать и уповать, что в новом 2024 году мы с вами еще много что там увидим.
P.S. С наступающим новым годом. Здоровья вам и вашим близким. И ярких и интересных праздников. А как они закончатся — ждите мои новые репортажи со всей нашей необъятной Родины
Прямо сейчас нас ждет процедура полимеризации. Вы готовы? Подождите, зачем вы тянете руки за нейроконнектором «Мысль». У нас в планах сегодня чуть другая полимеризация. Полимерная вакцинация из «Атомного сердца» это хорошо, но работа агрегата полимерных покрытий на Череповецком металлургическом комбинате еще лучше (и современные умные технологии и нейросети тоже будут). Заодно пора опровергнуть мемасик из двухтысячных и показать, что у нас в стране с полимерами все хорошо :)
Готовы? Тогда отправляемся в цех покрытий металла №3. Именно тут на сталь наносят полимерные покрытия (а в соседнем помещении и оцинковку делают, но это у нас в планах через пару дней).
Все начинается с двух разматывателей. На них подаются рулоны стали. Откуда они берутся? Рекомендую прочитать мои предыдущие посты, особенно про стан «2000»
Рулоны разматываются и подаются на линию агрегата. Вес такого рулона может доходить до 30 тонн
Зачем сразу два разматывателя? Это нужно для непрерывности производства. Пока один разматывается, второй уже устанавливается.
Лично для меня самый интересный момент на начальном этапе это сшивка рулонов. Именно благодаря этой процедуре мы получаем практически бесконечное металлическое полотно.
На всем агрегате установлено огромное количество датчиков. И если в недалеком прошлом все приходилось делать на глаз, то теперь все параметры измеряют лазерные датчики.
Благодаря получаемой от них информации, на концах рулона гильотинными ножницами вырубаются участки, с помощью которых на сшивной машине один рулон крепится к другому с помощью специального пресса и так до нужного момента, пока не надо будет заменить материалы для нового заказа.
Объединение происходит за счет создания двух рядов замков и дальнейшего их закрытия.
Оператору остается только проверить качество полученного шва.
Далее металл поступает на входной вертикальный накопитель. Если вы видели на фотографиях высоченный станок, более похожий на многоэтажный дом — это именно он.
Вместимость такого накопителя — несколько сотен метров.
С него полоса подается на участок обезжиривания. Он нужен для удаления всех загрязнений с металла.
На первом этапе происходит щелочное обезжиривание полосы. Далее очистка щеточными роликами, промывка деминирализованной водой в специальных емкостях, обдув воздухом. И в финале сушка полосы в сушилке.
После всех процедур по обезжириванию лента поступает на участок конверсионного покрытия. Там на двухвалковой машине наносится химический раствор (на одну или обе стороны)
Слой, образовавшийся в результате этой процедуры, повышает коррозийную стойкость. И адгезию металла с полимерным покрытием.
Теперь лента попадает в помещение коутера. Мы с вами можем увидеть происходящее там только через стекло.
Тут на нашу металлическую полосу наносят слой грунта.
На роликовых машинах в зависимости от требований заказчика могут нанести разные виды лакокрасочных материалов. Уровень блеска тоже корректируется в зависимости от пожеланий.
Сначала наносится грунтовочное покрытие на обе стороны нашего металла, после чего наносится уже второе покрытие.
Металлу пора в печи сушки. В цехе их две. В каждой по 5 горелок (а сама печь 54 метра)
За печами ванны с деминерализованной водой.
В первую печь наша лента попадает после нанесения грунта. После процедуры она по специальной линии возвращается в помещение коутера, где наносится лицевое покрытие. Далее во вторую печь для сушки.
Лента теперь будет поступать на вертикальный выходной накопитель. Он по размерам как входной, но выходной :)
Готовая лента поступает в помещение инспекции полосы. Ее ждет аттестация.
Может вы помните, что в моих репортажах с текстильных производств очень часто была история и фотография, как несколько сотрудниц стояли возле бесконечно движущейся полосы ткани и искали там брак. На мой вопрос, а нельзя ли на этот функционал поставить роботов и технологии, мне всегда улыбались и говорили, что человеческий глаз лучше всего подходит и вообще я ничего не понимаю в колбасных обрезках.
Но как оказалось, на «Северстали» вложили денежки и теперь людям часами не надо стоять у полотна и искать возможные мельчайшие элементы брака.
Я же обещал вам рассказать про современные технологии — получите и распишитесь.
На комбинате существует система автоаттестации Sherlock (даже интересно, какой персонаж детективов и за какие качества вдохновил разработчиков на такое название)
Разрабатывать проект по цифровому контролю качества начали создавать еще несколько лет назад . Полное его внедрение запланировано через 3-5 лет.
Проанализировав большое количество данных поняли, что человеческий фактор повышает вероятность пропуска брака. Как было сказано в одном фильме: «Все мы немощны ибо человецы суть». И его постарались минимизировать. Заменив человеческие глаза видеокамерами, фиксирующую всю поверхность.
К ним они разработали систему измерения в потоке. Так что в следующий раз когда на текстильных предприятиях мне будут затирать, как глаз-алмаз отслеживает все на ткани, движущейся со скорость несколько десятков метров, я буду орать гиеной.
Кроме этого создали прогнозную модель, «предсказывающую» по ряду показателей наличие дефектов, находящихся внутри полосы металла. Она создана, поскольку даже видеокамера на такое неспособна.
Отдельно работает система слежения за металлом, фиксирующая местонахождение продукта по узлам агрегата в каждую единицу времени. К ленте металла (да и к продукции других цехов тоже) привязываются снятые измерителями данные. Так что потом можно найти и удалить проблемный участок.
Данные по итоговой автоаттестации поступают оператору, а тот в свою очередь решает как действовать дальше.
Sherlock обеспечивает контроль 100% продукции и минимизацию ошибок, связанных с человеческим фактором и обладает инструментами для поиска первопричин отклонений по качеству, анализа трендов и построения моделей, обеспечивает доступность данных для любого пользователя и возможность быстрого подбора заказов для продуктов и продуктов для заказов.
По данным комбината с 2018 по 2022 доля поступивших претензий по видам продукции, охваченных системой, снизилась на 55%.
На выходном участке удаляются швы, которыми соединялись ленты. После она на автоматическом режиме заходит на моталку и появляется рулон готовой продукции.
С помощью крана рулон отправят на упаковку.
В цехе есть своя большая лаборатория, в которой проверяют качество металла и покрытия. Это делается по множеству параметров и напоминает настоящее колдунство.
Данные каждой проверки заносятся как в электронном виде в базу, так ив бумажные журналы.
Вот такая у нас с вами получилась интересная полимеризация с бонусом современных технологий.
Потерпите несколько дней и вас ждет ванна с расплавленным цинком и другие вкусности.
P.S. Ваш царский-королевский лайк и подписка мотивируют меня не валяться на диване и отправляться на новые производства. Верую и уповаю, что вы их не пожалеете
Несколько часов назад вернулся из Кинешмы. Заезжал фотографировать строительство их новых очистных сооружений и еще несколько объектов. И чудом удалось попасть на предприятие, производящее рабочие перчатки.
А что я делаю оказавшись на подобном объекте? Начинаю все узнавать подробно и с фотиком наперевес бегать, дабы самому наполниться новыми знаниями и вам показать.
Так что прямо сейчас мы увидим весь цикл производства хлопчатобумажных перчаток с покрытием из поливинилхлорида.
Но начнем мы с вами с небольшой познавательной странички. Она очень пригодится нам для понимания антуража на некоторых фотографиях.
Осенью прошлого года появилась информация, что одно из старейших (1879 года запуска) предприятий нашего региона — кинешемская ткацкая фабрика «Томна» прекратит свое существование. И 400 с лишним сотрудников пойдут на улицу (при населении города в 77 тысяч человек).
Сказать, что это был пипец регионального масштаба — это ничего не сказать.
Глава города и руководитель региона стали прикладывать все усилия, чтобы предотвратить приближающуюся катастрофу. И к великому счастью у них это получилось. На бывший комбинат приходит инвестор.
В начале этого года предприятие выкупает «ЛидерТекс». Состояние доставшихся им цехов не просто аварийное — это адок (отдельные слова благодарности за такое герою комикса "Сова - эффективный менеджер", который видимо трудился на прошлом предприятии). Даже сделал вам кадр одного из них, до которого еще не дошли руки при ремонте.
Цех за цехом начинают ежемесячно подготавливать к работе.
Весной устанавливают полторы сотни вязальных станков (сейчас их уже более 600).
Более двухсот сотрудников старого предприятия переобучают в Иванове и трудоустраивают на новое производство. Еще сто человек нанимают дополнительно.
Для чего был мой рассказ? Не с целью похвалить владельца группы компаний, выкупивших останки комбината и воссоздающего одно из старейших предприятий по кускам (хотя это реально крутой дядька).
Моя цель объяснить, почему в цехах на новом производстве не евроремонт, а затертые стены и полы.
Верую и уповаю, что получится постепенно восстановить весь комбинат и создать еще сотни рабочих мест.
Но давайте вернемся к перчаточному производству.
Для производства перчаток используют хлопчатобумажную пряжу. Манжет перчатки делается из синтетической нити или ее аналоге.
Более 600 перчаточных вязальных автоматов установлены в цехе.
На них выпускают рабочие перчатки 10 и 7,5 классов (по 4,5 и 6 нитей). Их модель задается заранее на станке.
На станке вяжется само изделие. Все происходит автоматически. Вяжется перчатка начиная с мизинца.
Манжета перчатки обметывается.
Вязальный станок отправляет перчатку в корзину по ее готовности.
Но где же наносят всем нам знакомые по стройке и субботникам пупырки :)
Главная магия происходит на карусельных станках.
Именно на них и наносится ПВХ.
Полученные с вязальных станков перчатки одевают на металлические заготовки.
Чан с ПВХ покрытием уже готов поделиться своей начинкой с карусельным станком.
ПВХ наносится автоматически
И уже готовая перчатка отправляется сохнуть, а потом в упаковку.
Огромные пакеты перчаток отдыхают на складе и ждут своего будущего покупателя.
Несколько месяцев назад на предприятии стали восстанавливать ткацкое производство. Главная цель на ближайшие годы восстановить полный цикл производства на комбинате.
Очень хочу через несколько лет приехать опять на комбинат и показать как он изменился (надеюсь, что только в лучшую сторону)
А еще хочется пожелать кинешемцам побольше рабочих мест и новых производств больших и не очень.
P.S. Если интересно посмотреть очистные сооружения 70 тысячного города — сделаю отдельный пост.
Хоть раз в жизни вы слышали этот звук. Словно у соседей сверху падает металлический шар, а потом они катают его по полу. На кой фиг им такое развлечение всегда оставалось тайной.
Самое веселое, если это происходит ночью. Только начинаешь проваливаться в сон, а тут с потолка такая радость раздается.
В детстве мне казалось, что это просто соседи у меня упоротые, но с появлением интернета оказалось, что я не один такой «избранный», и десятки тысяч людей пугались/просыпались от подобных катаний.
Судя по огромному количеству запросов в поисковиках, всем интересно, а что же это такое на самом деле? Чаще всего в качестве объяснения предлагают следующую научную версию: днем дом нагревается, арматурный каркас в нем чуть деформируется (пруты чуть изгибаются) из-за теплового расширения. Когда же наступает ночь, происходит охлаждение и арматура возвращается в исходное положение. Все это сопровождается знакомым до невроза звуком.
Вроде все понятно и очевидно. Но что если и правда кто-то катает стальные шары по полу.
Но откуда возьмутся большие металлические шары для подобной процедуры? Оказывается их производят в промышленном масштабе.
Для чего, из чего и как?! Давайте разбираться вместе.
Мы уже несколько дней с вами изучаем Череповецкий металлургический комбинат. В одном из его многочисленных цехов и установлен шаропрокатный стан. Именно на нем и выпускают мелющие стальные шары десятками тысяч.
Они служат для измельчения хрупких, сыпучих, крошащихся материалов с помощью барабанно-шаровых мельниц.
Окажись мы на горно-обогатительной фабрике, то увидели бы, что подобная мельница работает следующим способом: огромный барабан вращается вокруг своей оси, в него загружается материал для измельчения и огромное количество стальных шаров. Шары поднимаются, после чего в падении ударяют по материалу, а тот измельчается(это если максимально просто и понятно, так процесс намного интереснее).
Теперь же посмотрим на сам производственных процесс.
Шаропрокатный стан №3 самый новый на комбинате. Запущен в 2020 году.
Что он из себя представляет: нагревательную печь, клеть, отсеивающий барабан, подсуживающий барабан, закалочный барабан, вертикальный транспортер, печь низкотемпературного отпуска, а дальше соответственно фасовочная зона.
На стане производится продукция диаметром от 60 мм до 100 мм
В цехе используется горячекатаный прокат круглых заготовок.
Стальные заготовки доставляют в цех (их получают в другом цехе со стана 350). Прутки приходят диаметром равнозначным будущей выпускаемой продукции.
Прутки попадают в печь и нагреваются газом (конкретно в этом цехе так, а индукционный нагрев есть в других цехах ШПС-1 и ШПС-2).
Заготовка равномерно разогревается по всему объему и длине. Температура задается в зависимости от марки используемой стали ( до 1120 градусов)
После этого металл попадает в клеть, а после в отсортировачный барабан
С помощью трехзаходных валков металлический пруток диаметром 60 мм за 1 оборот клети «отрезает» от себя 3 шара. На обычных валках за 1 оборот — 1 шар.
Сами валки находятся в клети, но мы можем увидеть валки под другие диаметры прутков вне работы. Под каждый диаметр используется своя пара валков.
После выхода из клети шары попадают в сортировочный барабан.
На пути к нему отсеиваются не сформировавшиеся шары.
Когда смотришь на этих раскаленных красавцев, появляется ощущение, что смотришь на производство апельсинов или витаминок-аскорбинок :)
Не знаю откуда у меня такая любовь к раскаленному металлу, но я залипал бы около этой «карусели» максимально долго.
Стальные шары подаются через воздушное охлаждение. Далее их ждет закалочное устройство, где они охлаждаются до определенной температуры конца закалки шара.
Теперь им предстоит попасть в печь низкотемпературного отпуска, для снятия напряжения в закалочном устройстве.
Впереди визуальный контроль. Сотрудник осматривает шары, и если видит брак — удаляет его с ленты
Остается только все погрузить и отправить на склад.
Так что если вы услышали дома шум от соседей, то или виновата арматура в полу или у них откуда-то стальные мелющие шары :)
Вот такая небольшая познавательная экскурсия получилась в один из цехов Северстали.
Впереди нас ждет агрегат полимерных покрытий металла и цех с высокопрочной оцинковкой. Так что как принято говорить на ютубе — лайк, подписка и до встречи в ближайшие дни!
Череповецкий металлургический комбинат по своим размерам напоминает небольшой такой город. Даже если вы тигриный-лев и любите прогулки, то за неделю не получилось бы обойти все его цеха и производственные базы. И если никогда до этого вы не видели таких огромных производств — то небольшой приятный шок вам гарантирован.
Но мы с вами постараемся объять необъятное, поэтому в ближайшие дни побываем в наиболее интересных цехах.
Сегодня нас ждет красавец-гигант: километровый непрерывный полосовой стан горячей прокатки «2000» в листопрокатном цехе №2. Это один из ключевых производственных объектов ЧерМК и при этом он один из самых производительных станов горячей прокатки в России.
Длина линии – более километра. На нем производится больше 6 млн тонн металлопроката в год - 65% товарной продукции комбината, более 350 видов сортамента для теплоэнергетики, оборонной и автомобильной промышленности, судостроения и машиностроения.
Чаще всего на такой объект попасть можно только после 100500 миллионов согласований, но с 2019 года он стал являться часть маршрута тура по промышленному туризму в Череповце (и это в два раза увеличило количество экскурсантов в регионе по такому профилю). Для желающих полюбоваться на раскаленную сталь в цехе даже оборудовали смотровую галерею протяженностью 30 метров, находящуюся на высоте 10 метров (спасибо Северстали за такой подход). Так что они могут в безопасности на все это взирать. Мы же с вами своими ножками все обойдем и посмотрим на все намного ближе.
Но давайте вернемся немного назад. Вчера мы с вами видели как в доменной печи образуется чугун. Чугун это хорошо, но сталь нам нужнее для дальнейших процессов. А ее производят как раз из чугуна, путем снижения количества углерода, фосфора, серы, марганца.
Ковши, наполненные чугуном, отправляют в кислородно-конверторный цех, где они уже и станут сталью.
На стан 2000 сталь поступает в виде слябов — большой стальной заготовки.
Разогретые в печах до тысячи с лишним градусов слябы попадают на километровую линию. Создается ощущение, что ты стоишь рядом с рекой лавы.
Менее чем за 4 минуты «толстенький» сляб толщиной 250 мм станет полосой металлопроката в километр длинной
Слябы выходят из печей каждые 40 секунд. Еще совсем недавно время их выталкивания определял оператор, и иногда паузы продолжались до полутора минут. Теперь же за все отвечает автоматика. Только за три месяца работы цифрового помощника удалось избежать простоев на 27 часов, (дополнительно удалось получить 24000 тонн металлопроката)
На стане производится металл для оборонки, автомобилестроения, судостроения, ТЭК, машиностроения и электротехнической промышленности.
Сам цех был запущен в далеком 1975 году. Но все оборудование в нем постоянно модернизируется и обрастает новыми средствами автоматизации.
Например, в прошлом году ввели в эксплуатацию новую нагревательную печь №1, а за год до этого новую нагревательную печь №2.
Их производительность в два раза выше, чем у прошлых: на холодном всаде – 400 тонн в час, на горячем – 500.
Благодаря им снижен уровень расходного коэффициента металла, а также расход газа.
Но давайте пройдемся дальше.
После каждого этапа на стане слябы становятся все тоньше
Мне кажется, что благодаря размерам цеха трудящимся не нужно ходить в фитнес клубы, они и так в день спокойно могут находить до 25 км :)
Огненно-оранжевый металл так и манит — прикоснись ко мне. Если бы не его температура в 800 с лишним градусов, точно бы потрогал.
Прокатные валки делают металл все тоньше и тоньше
Бесконечно можно смотреть на три вещи: как горит огонь, как течет вода и как в кассе выдают зарплату. У сотрудников цеха есть в прямом доступе все эти элементы.
На пункте контроля несколько операторов следят за всеми показателями стана. Ощущение словно оказался в рубке космического корабля.
Огромная установка служит для ускоренного охлаждения.
Как уже говорил — весь стан наполнен разнообразными датчиками. Но о системе управления качеством продукции мы поговорим отдельно, когда окажемся на участке отделки листа в цехе покрытия металла.
Финальный этап работы стана — смотка рулонов
Даже в берушах гул в этот момент ощутим. Сначала даже пугаешься, когда километровый лист металла на высокой скорости скручивается.
Полученный рулон отправится или на склад или на следующий этап обработки (на котором мы побываем вместе с вами уже а ближайшие дни)
Масштабы цеха поражают. Больше я пока не видел.
Слова благодарности хочется сказать всем бывшим и действующим сотрудникам этого предприятия и других заводов в стране за их сложный, но такой важный труд. В который раз для себя убеждаюсь, что именно такие люди труда круче всех супергероев из комиксов и фильмов в сотни раз.
"Не переключайтесь, новый цех уже скоро"
Сегодня хочу познакомить вас с самой горячей череповчанкой в Вологодской области (а может и во всей стране). Прежде чем показать ее фотографии, немножечко опишу, дабы вы могли сами ее себе вообразить, а потом уже сравнить с результатом.
Она очень высокая (около 80 метров в верхней точке), с отличной фигурой (площадь центрального узла 71000 квадратных метров), из многодетной семьи (еще есть две сестры — Северянка и Вологжанка), обожает современные технологии (один только 3D-профилемер в куполе чего стоит, а уж датчиков везде — огромное множество), очень мощная (3000000 тонн чугуна в год для нее не предел). Разве не красавица?
А теперь пришла пора познакомиться с ней поближе. И для этого нам придется прямо сейчас направиться во второй по численности город в Вологодских землях — Череповец. И пока я буду лететь туда на самолете (в регионе аж целых три аэропорта), вы успеете заварить себе кофейку и даже вкусняшку какую приготовить...
Наступила пора познакомить вас с этой красавицей. Заезжаем на территорию Череповецкого металлургического комбината, где нас ждет наша «Череповчанка».
На фото если что не она, а Алёна — журналист из электронного издания, которая тоже приехала посмотреть на огненную красавицу из Череповца.
А вот и наша героиня: Доменная печь №3, получившая имя «Череповчанка». И она реально очень-очень горяча, даже чугун в ней разогрет до полуторы тысячи градусов)
В последние годы очень модно говорить, что фабрики и заводы у нас не работают, и что кроме березового сока и лаптей ничего у нас в России не производят. Очень хочется смеяться с таких высказываний, особенно когда приезжаешь на огромное производство.
Для примера: население Череповца 300 тысяч человек. А сколько из них трудится на предприятиях только «Северстали»? Более 23 тысяч человек. И в городе есть еще крупные производства (кстати, гвозди в Череповце тоже делают, хоть многие одно время утверждали, что у нас и гвоздей своих нет, но это совсем другая история)
А еще крайне интересно смотреть на людей труда, работающих в несколько смен в разных отраслях промышленности, ведь по мнение отдельных диванных критиков их нет, а они же в свою очередь спокойно каждодневно трудятся, и даже не знают, что некоторые особо одаренные даже не знают про них (или закрывают глаза и не хотят видеть действительность)
Вернемся к нашей «Череповчанке». Зайдем в ее сердце — Центральный Пульт Управления.
Возводить «Череповчанку» стали в 2018 году, а в 2020 уже задули (таким термином обозначается старт подачи воздушного дутья в доменную печь).
На ее строительство потратили 34 млрд. рублей. Для понимания насколько это серьезная сумма инвестиций — годовой бюджет Вологодской области на 2023 год — 111,636 млрд. рублей.
Как я уже говорил в самом начале — на разных узлах печи установлены датчики, вся информация от них сразу поступает на десятки экранов Центрального пульта.
Все максимально автоматизировано, на многих этапах работает техника, и если несколько десятилетий назад на таких же по размерам доменных печах трудились до 8 сотен человек, то теперь их нужно лишь 200 с небольшим.
Смена газовщиков (а именно так называются сидящие у экранов специалисты) — 12 часов.
Работа безусловно сложная. Лично мне кажется, что не каждый человек смог бы ее выполнять, поскольку тут необходимо множество качеств и не только внимательность, реакция и усидчивость.
Комната отдыха находится рядом с их рабочим кабинетом и выглядит просто волшебно.
Но давайте уже пройдем к раскаленному чугуну и этому металлическому пламени.
Спускаемся в литейный двор после еще одного инструктажа.
И оказываемся в нереальном пространстве.
Сложно поверить, что все это создано руками людей, а не какими-то древними атлантами.
В какой-то момент мне начинает казаться даже, что я в мире-кузнице Марса из вселенной Warhammer 40000. Постоянно ждал, что сейчас подойдет представитель Адептус Механикус и направит меня на строительство нового Легиона Титанов :)
Но в реальности ко мне подходили не менее крутые люди, жизнь которых десятилетиями связана с профессией горнового.
Ощущение рядом с раскаленным чугуном просто космическое. Словно стоишь у жерла вулкана. Искры гипнотизируют. Видимо, наш вид с древности настолько воодушевился огнем, что теперь любовь к нему зашита в подсознании.
Но я увлекся эмоциями, давайте лучше расскажу технологический процесс, благодаря которому и получается чугун.
Шахтеры добывают уголь. Тот в свою очередь попадает на обогатительную фабрику — не подумайте, что там в него кидают деньгами и делают его богаче. На самом деле его дробят и убирают все, что не является углем. Итогом является угольный концентрат.
Именно этот концентрат и поступит на коксохимическое производство. При этом есть целый ряд марок такого угля, которые необходимо смешивать, но это если сильно-сильно углубляться. Нам же более общий процесс интересен.
Смесь концентрата запекают в коксовой батарее при температуре чуть более 1000 градусов. При этом не дают доступа кислорода. На выходе уже готовый, но раскаленный кокс. Его необходимо теперь остудить.
С коксом все понятно.
А как быть с рудой? Ее тоже обогащают, но своим способом.
Далее руду смешивают с коксом (получается шихта), после чего с помощью подъемников направляют в доменную печь через засыпной аппарат.
Снизу вдувается раскаленный воздух и газы, а сверху движется шихта.
Постепенно эта смесь спускается все ниже и превращается в шлак и чугун (температура повышается, руда плавится, железо соединяется с углеродом).
Чугун выпускают через летку чугунную, а шлак над чугуном соответственно выпускают через летку шлаковую.
Полученный чугун направляют для дальнейшей переработки. Шлаки тоже не выкидывают (про дальнейшую переработку если вам будет интересно, то сделаю еще посты, просто есть ограничение по количеству фотографий)
На перчатке лежит проба чугуна, полученная горновым. Разумеется она остыла уже и не представляет опасности. (если бы не остыла — пришлось бы искать доктора Айболита и пришивать другую руку)
Пробы чугуна берутся несколько раз при каждой плавке.
Горновой берет ковш (ложку для отбора проб) и делает отбор. После которого проба сразу направляется в лабораторию.
Самое интересное, что все сотрудники относятся к доменной печи как к живому человеку. И в разговорах упоминают, что если с ней хорошо обходиться, то и она ответит таким же образом (даже когда заступают на смену с ней обязательно здороваются). Очень необычно такое видеть, но есть в этом что-то особенно душевное.
С «Череповчанкой» мы познакомились, а через несколько дней побываем на Стане 2000 в листопрокатном цехе, на агрегате полимерных покрытий и в других интересных локациях. Так что «не переключайтесь и оставайтесь с нами» :)
Если бы меня кто-то попросил описать одной фразой павильон «АТОМ», на ВДНХ, то я сразу бы ответил не задумываясь цитатой из отечественной кинокомедии режиссёра Романа Качанова «ДМБ» : «- А может бахнем? - Обязательно бахнем! И не раз! Весь мир в труху!.. Но потом...». Она идеально подойдет в качестве характеристики довольно крупной части этой выставки.
Если же хотите подробностей, то напилил немного фоточек и расскажу чуть про эту необычную локацию
Насмотревшись художественных фильмов «Оппенгеймер» и«Сахаров», восхотелось мне чуть ближе прикоснуться к этим событиям. А поскольку допуска к архивам и гостайне у меня нет, то нужна была какая-то альтернатива. Тут мне на помощь пришел РОСАТОМ, со своим колоссальным просветительским комплексом с большой-пребольшой экспозицией, посвящённой ядерной энергии. А с учетом того, что посмотреть ее до середины апреля можно за ноль рублей — грех не воспользоваться таким предложением (особенно когда в Москве бываю довольно часто и пару часов времени для такой радости могу выделить).
Заходим на ВДНХ и двигаемся от центрального входа в сторону 19 павильона. Мобильное приложение выставки с картой, так что не потеряетесь — если же сел телефон, то просто идите прямо от центрального входа до фонтана и дальше и там точно его не пропустите, вас остановит большой стеклянный куб с 12 метровыми окнами. На их производстве мы с вами были в Челябинске и тогда отдельные товарищи спрашивали, а зачем большие стекла, не надо никому такого, а вот оказалось, что у архитекторов и заказчиков свое мнение на этот счет...
Внутри на терминале получаем бесплатный билет и добро пожаловать на экспозицию, размещенную на 25000 квадратных метров.
Строили всю эту красоту 6 лет. А поскольку наземная часть здания из-за ряда требований не могла расти как высотное здание, то будущий павильон прирастал подземными этажами. И когда оказываешься в самом низу и понимаешь где ты, немного даже оторопь берет.
Перемещаться между уровнями помогут эскалаторы. Лифт тоже есть, но я им не воспользовался — очередь была. Очереди это вообще отдельная песня на выставке «Россия». По этой причине рекомендую оказаться там с понедельника по четверг и желательно часов до двух дня. Оказавшись внутри смотрите что угодно — нет каких-либо требований по посещению залов, так что если в одном толпа — сходите пока в другой зал. Каноничным же считается посещение от прошлого к будущему. От подземного зала «Советский атомный проект» до «Атомариума» на самом верху.
Лично для меня экспозиция про историю нашего атомного проекта со всеми учеными, разведчиками и специалистами самая интересная часть «АТОМА». И сразу видно с какой любовью и вниманием там все делали. Это не просто копии документов и фотографии — вас ждут целые восстановленные помещения от секретных институтов до квартир граждан СССР и США. От вагонов с ураном до огромных копий бомб. Единственное что немного расстроило, что не нашел ничего про проект мирных подземных атомных взрывов на территории СССР (хотя может проглядел), дело в том, что один из них на объекте Глобус-1 происходил в Ивановской области, но это совсем другая история.
Если подняться на этаж выше, нас будет ждать экспозиция «Время первых», охватывающая несколько десятилетий после 50 года. Тут уже царит мирный атом — начиная от атомного ледокола и заканчивая разнообразными фантастическими проектами (многие из которых остались только в чертежах, но на выставке сделали их макеты).
Рядом расположена «Аллея знаний» с библиотекой, лаунж зоной и горой других активностей, но у меня не было времени на отдых, так что я продолжил метаться по павильону как сайгак.
Выставка «Современная атомная промышленность» про современные технологии и разные разработки в сферах от медицины до экологии. Мне показалось, что это больше похоже на визитку РОСАТОМА. Но с учетом всего павильона, пусть хоть пять таких рекламных штук сделали бы.
И финал «АТОМА» это «Атомариум». Туда пускают с экскурсией (нужен отдельный билет и до апреля он тоже бесплатный), так что в следующую поездку обязательно загляну туда на 45 минут.
Так что если собираетесь в Москву — обязательно сходите. Лично я еще несколько раз туда постараюсь заглянуть и провести больше времени, внимательнее погружаясь в тематику.